Monday, January 30, 2006
Busy Weekend
The front triangle is finished except for some sanding. It looks good and straight. The BB went much better than in the past - in part because it's much easier to do a really good job of pinning the joints in a jig. Everything is held securely in place while setting the pins, so there's no risk to setting the pins firmly. One tube in the BB needed some touchup work. All the joints flowed through nicely, but the one flowed a little too much and left a slight gap at the edge where I was feeding the silver. That's taken care of now.
Very little cleanup filing was required - mostly just the pins on the inside and outside of the tubes. The angles and BB height all checked out fine, so I moved onto the chainstays. They're going to be fairly long (430mm). The first one went in great, but the second one seems to have got a little out of alignment - and needs some additional work. I think I'll drill out the pins, reheat the joint and reposition the stay. Hopefully I won't need to do any further cosmetic fill when this is done. I could probably just cold set things, but I don't want to go that route.
Reynolds is shipping me some pre-bent fork blades which should be here soon. Probably a pair of these will be coupled with a HJ fork crown with a built-in 3 degree rake. I'll make up two forks resulting to different trail figures to see how each works.
That's it for now. Time to swap back to Carbon 1 and get it done and out the door.
Cheers
Friday, January 27, 2006
Need some more pictures of the final product
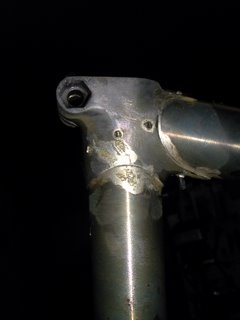
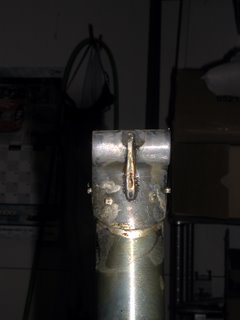
I can see that while these are clipped and have had the flux soaked off, I don't have any pictures showing the lugs after filing off the pins. Maybe tomorrow.
If you're curious about what's happened to Carbon 1, its an issue of running out of epoxy. I like how the filets are building up at the joints. While this is non-structural, I want to complete this process to get the nicest possible finish - but the epoxy ran out. Should have some tomorrow - so then back to Carbon 1
Some post-clean-up pix
Thursday, January 26, 2006
Backwards Order
Some Pictures Finally
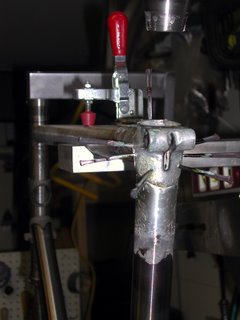
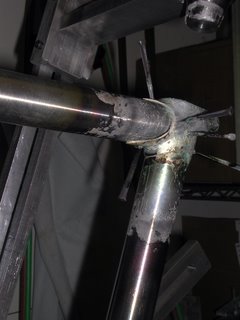
Well, here are some pictures of my latest frame project (010106). It's a sloping top tube road bike. The upper lugs are Henry James mountain bike lugs to get the slope. The bottom are Walter which give me the BB drop I want with 700C wheels. Also, the lower head lug has built-in ergo stops. Very cool.
I've been fiddling with joint fit and geometry. This is much easier with a jig than off drawings IMHO. Borrowing an idea from Nic Crumpton, I've clamped a piece of 1x1 angle channel to the the bottom rod that carries the head-tube cones. This gives a reference point for where the steering axis touches the ground. Thus its possible to ensure that the bottom head-lug is positioned properly for the chosen length of fork. Very nice.
Things were looking good tonight, so I took to filing down the seat-lug. It needed a lot of work because I didn't like parts of its shape. The seat-tube ends within the lug. There is a ring around the top of the seat-tube spigot, so its important to get one's seat-tube length right (see prior paragraph) as there's no leaving it to long and trimming later. Because of this design, the lug essentially has a flat top. There's probably a good engineering reason for this relative to mountain bikes, anyway I picked the lug so I'm not complaining. But, the transition from the sides of the lug to the top was a bit to amorphous for me. In fact the whole seat-tube barrel and the lugs for the binder bolt also seemed from a visual perspective to be a bit too much like pudding.
So, I spent a couple of hours with a file, and got a result that looked much better - especially when mounted on the tubes. Anyhow, everything was fitting fine, and I've had an itch to get the torch back in my hand, so I had a go at it.
First the usual cleaning of lug and tubes. Then drilling and fluxing. Finally pinning the joint and checking everything in the jig. Looking good, so on to some more flux, mount the joint in a work stand and have at it with the torch.
The pictures were taken after the finished assembly was put back into the jig to check fit. The jig isn't an alignment table, but things looked real good.
For having been away from the torch for a while, I was very pleased with the braze. There was a little bit of cooked flux on the crotch of the joint, but overall things looked good. The edges were clean and require no filing. Not to much silver was dripped in the wrong places. The edges are nice filled showing that I pulled the silver through well. There's a nice ring of silver at the end of the seat-tube inside of the lug. Cool.
Tuesday, January 24, 2006
Bugs
Anyway, things are progressing slowly in the shop. Most of the sanding of filets is done. Tonight should finish up everything but the BB cable guides. After the guides it will be on to the paint shop.
Speaking of guides, I purchased 1 - 3/16x6" stainless steel tube, 1 - 5/32x6" stainless steel tube, 1 - 3/16x36" brass tube, 1 - 5/32x36" brass tube, and 1 - 3/16X36" aluminum tube. All of these are intended for experiments in BB guides. I'm not sure yet which will go on the bike. Part of the issue is what is required fit this into the couplings that bisect the base of the chainstay.
The 5 little pieces of metal came to a bit over $36. The lady ringing things up at the hardware store did a double take, and asked me if I was sure I wanted all these tubes given their price? I said, no that everything was OK. But, boy are those little suckers expensive at the hardware. Once I have things sorted out, I'll have to purchase quantity from an industrial source.
What I want to try is to flare the end of a tube so that it "fills" the hole in the bushing I've placed in the top of the chain stay. Then I'd like to bend the tube as it exits the lower bushing and epoxy the tube to both bushings and at the front to the bottom of the bottom bracket.
An alternative under consideration is a stainless sheet bent around the bottom of the bottom bracket, which is glued and riveted to the BB. With a rolled edge, the cables should stay on this sheet, and the front of the chainstay tube could be brazed (off the bike) to this plate. The sheet would serve to keep the cables from digging into and damaging the carbon around the BB.
All of this should be the subject of some fiddling tonight. I'll keep you posted on progress.
Wednesday, January 18, 2006
ZZZZZZZZZZzzzzzzzzzzzzz...............
I've been getting too little sleep and am sometimes relying on excess enthusiasm to keep moving. :)
Work continues to be big, but things are also moving along in the shop. I'm cutting out early to interview some painters for Carbon 1 (whoops, went on a showing instead). It's just about ready for them, with the joint filets looking pretty sharp. The Cane Creek IS-8 arrived. I did a test install of the fork. One thing about an integrated headset, it's easy to install. I got the version with a tall carbon spacer and it looks much like the Record with it's tall carbon spacer. I trimmed the steerer correctly the first time. Cool! Now the fork is safely packed away in its protective bubble wrap until the bike gets built up.
Speaking of trimming steerers, the Park tool for cutting threadless steerers is a great way to get a square cut on any tube. It's much easier than trying to free-hand the hacksaw through the tube. That means a lot for building stems.
Joe is waiting for dimensions from me to build a trunnion for my jig. The problem is, I thought it just went into the clamp of the Park stand. Wrong. It replaces the clamp. My clamp attaches with what is essentially a big conical nylon bearing that fits into a female fitting on the stand. At the center of the cone is a threaded shaft. This is used to pull the bearing into it's fitting, and to lock it from spinning. So, Joe needs some dimensions - but I don't know where to begin. It's probably time to give him a call.
Joe got me my new lower head lug, so I've finished fitting the downtube on my new sloping top-tube bike. Essentially, the seat tube will be my usual length, but the stem/handlebars will be located higher. If you've looked at the pictures below (of my current bike), this will make sense. So, pinning and brazing soon.
Meanwhile, it doesn't make sense for me to have two bikes underway at once, so I'm going to concentrate on sanding down Carbon 1 and getting it off to the painter. But to be honest, I'm more excited about the steel frame. I really want to see how much my craft has progressed since the last one.
Tonight is math-night at school with the twins, then early to bed. Tomorrow I have to figure out my painter. Friday night should finish prep on Carbon 1, and the its on to frame 010106.
Cheers,
Saturday, January 14, 2006
Carbon Carbon Everywhere
Anyway, I've been sanding the down the frame in anticipation of paint. I got about three-quarters of fit done. It's been decided that most of the Deda decoration on the rear triangle will disappear. We'll just keep a small "Dedacciai" at the rear end of each chainstay.
All but one of the cable/ergo stops are mounted. For this frame, the ergo's are on the sides of the down tube (next time I may try the underside). They need to be perfectly positioned to be symmetrical. So, I'm taking my time in positioning the last one.
The frame takes an integrated headset. Too bad, because there isn't an integrated headset standard. What should be the right headset is in the mail, along with an FSA gauge that will help me make sure. Ah well, sooner or later we'll sort that out.
I mounted water bottle bosses in the top and bottom of the monostay on the chainstay. There are to route the front derailer cable. The carbon is so thick here that there can be very little rivet effect. Maybe if I had some bosses that were twice as long. However, they are also epoxied into place and unlikely to move for a very long time. Next will come the under bottom brake guide. Finally, I've also applied some epoxy to fair in the joints between the major portions of the frame. I think that's going to look real nice.
My neighbor brought by his teams jersey, so we can find some match paint colors. A big stripe will run across the frame in these colors - hopefully that'll generate some sales. Net of all this, I'm almost ready for the paint shop. It's going to be fun to see how it all turns out.
I'll keep you posted.
Friday, January 13, 2006
Brrrr!!!!
Waking up the temperature was 38 and it was raining. With fenders and a raincoat things should be fine. It was to be an interesting test of bike and rider.
Starting out, with the wind at my back, the ride was very pleasant. There was no rain on my face and the fenders keep the road water where it belonged, even when riding through puddles. At the turnaround, things got nasty. The temperature had been falling and the rain drops were turning to ice. Little daggers were attacking my face and I had to keep my windward eye shut. It was also at this point that I realized that my winter gloves weren't waterproof. Wet fingers and the now freezing temperature combined to make my digits numb. It was hard to work the shifter, small motor skills were declining. Each finger would take a turn in the heart of the glove to to take the edge off the numb, and then swap for another. This strategy was staving off the worst, but hardly a substitute for warm hands.
It was here that the bike showed what was right about its design. When physical discomfort or fatigue set in, little issues get magnified. An uncomfortable seat, tendonitis, poor fit, will all begin to feel unbearable. But there was none of that. Moreover, when a rider is tired or sore or, in my case, suffering from a lack of feeling in the hands, bike handling and stability become much more important. I could concentrate on keeping my hands from freezing and trust the bike to get me home - and when you're on the edge, thats a nice feeling.
The bike was changed, however, since the last ride. I'd replaced my aerohead wheels with a set of MA3 on record wheels. My skewers were missing and I replaced these with a set of American Classic skewers from ebay. And from there came my second problem of the ride. The rear skewer just didn't want to hold my rear wheel in place. Eventually I tightened it more than seemed prudent, but it held. At that point it also became clear that there isn't any positive lever stop for the closed position. It appeared I could keep closing the lever until it would hit the spokes (not an option that I tested). Moreover, that as the lever closed farther, it was over-center and thus at less than its maximal tightness.
In response, I twisted the lever so that it closed against the seat stay. This doesn't leave much room to grab the lever to open it. And it may rub off the paint on the stay. Obviously this isn't a long term solution. Now, I'll grant you that this is probably a poor skewer choice for the bike. After all these are very light weight as for a racing bike. Still, I didn't know that there could be such deviation in basic functionality of a skewer. Anyhow, these will probably go on the carbon bike to minimize its weight. Meanwhile, they will get some shop time to see if there is a tweak to improve them.
Shifting in the lower gears was a little off too. The wheels have an almost new cluster (again from ebay). But, I didn't expect it to give problems. When I looked back at it, I could see the problem. Starting from the big cog, the #2 & #3 cogs were spaced much closer together than the rest. I'm not sure why. But, there's another shop project.
So, a couple of minor mechanicals to deal with, but overall a solid bike for the ride. By the way, freezing fingers and all, this was much more fun than spinning class.
Ciao
Monday, January 09, 2006
Dedacciai Black Pearl
Busy Hands
I'm beat, but that's not all bad. Work is busy, so I'm making some money. And my second league of curling started with a win. But, the key thing is that I built a carbon bike this weekend.
I started with a Black-Pearl front-end and a Black-Box/Drive-Tail rear-end. This will be assembled with a Black-Drive fork. This is all top of the line Dedacciai carbon.
The first step was to mount the frame in the jig by the BB and top of seat tube so that the seat tube angle could be set correctly. Then, it was time to chose chainstay length. I went a little long for a more stable ride. Because the extra length comes from the monostay at the front, it shouldn't create too much flex. Then the bottom bracket drop was set with the dropout mount.
With this accomplished, the monostay and its socket (along with the stay ends and the dropouts) were preped by sanding well and then cleaning with a rag and acetone. The later was accompanied by gloves and a respirator. The 3M epoxy is an aerospace grade two part in black (to match the carbon).
The epoxy comes in cartridges with dual cylinders. This mounts to the front of a little handle which operates much like a caulking gun (but is much more precise - in fact its manufactured in Switzerland). A long mixing tube attaches to the front of the cartridge and can be replaced with a cap to save the remaining epoxy for later use.
The epoxy is a bit more liquid than I expected. This has two immediate consequences: a) it flows more easily through the baffles of the mixing tube than expected; b) it drips more easily than expected when applied to frame parts. The former is great and the later is manageable - so far so good.
Epoxy went on the socket and the monostay, they were pushed together, then the same with the dropouts and the dropouts were locked into the jig. Finally the acetone rag was used to clean off the excess epoxy. Well, that was easy. To facilitate curing, I positioned my portable heater under the frame (but not while the acetone was nearby).
Next comes the seatstays (also a monostay design). A post sticks out of the seattube, pointing toward the dropouts. It has a slight taper so that it is narrower at the lower end. The monostay is much bigger around with a triangular cross-section. A carbon fiber moulding that is triangular in shape with a small hole bored through the length fills the space between the the two.
Its necessary to sand down this filler to fit into the monostay and leave space for epoxy. I also mitered the one end to approximately fit the seattube. This was then epoxied to the monostay with the miter sticking out of the end. Next the dropout fittings were epoxied to the ends of the seat stays. These were loosely fitted to the dropouts and the top of the stays propped against the seattube until the epoxy was essentially cured.
Then the seatstays were unscrewed from the dropouts and I began the process of mitering the monostay to the seattube. For this, a 6" cutoff wheel was mounted in the drill press. First the tube was cutoff at the same angle as the filler (by eyeball). Then, using the side of the wheel, the miter was ground off a little at a time and carefully checked for fit in length and miter. After a patient process, a good fit was obtained. Then, the stay was popped into place.
This is a little tricky. The dropout fittings fit into a sort of a pocket in the dropouts. The best approach for sliding the monostay onto the tube on the seattube was with the stay ends below the dropouts. When it gets to the point where its necessary to slide the fittings up against the dropout, a little edge is in the way, and I had to slightly pull the stay ends apart to fit. Knowing the rigidity (and potential brittleness of carbon), this was a nervous time. But, it actually proved to be a quick easy process as everything popped into place.
Then having proved the fit, I had to pull this apart again, apply epoxy to the monostay, seattube, and support tube and put it back together again. Again, this proved easier to do than describe. Some more wipe up with the acetone rag (being careful not to pull epoxy from the joint) and I could screw the fittings into the dropouts. Actually, I put some medium thread-locker on the screws. Then the heater went under the frame again and I sat back to look at what I had. It looked nice.
After things had cured for a couple of hours, it was time to tackle the waterbottle mounts. Now there were only two problems with this plan: a) I'd never used this blind mounts before; b) it wasn't clear if the frame was designed to have them placed in any one position. After a talk with Joe, it was clear that I could mount them according to functionality and not the design of the carbon tubes.
So, I got out one of the mounts, put it into the tool (which came without directions) and did a practice application in thin air. Basically, this works much like a pop-rivet. The tool has a pair of levers which are squeezed like a pliers. On its head, there is a mandrel on one side. Sticking out through this is a narrow treaded rod.
The mount is screwed onto the rod. When the levers are squeezed, the rod pulls the mount toward the mandrel, and the back of the mount's tube crushes outwards. When pulled far enough, this crushed tube presses up against the back of the frame tube locking the mount into place. Hope that's clear.
So, I marked and drilled holes in the seat tube, applied epoxy to the holes, and had at it. The epoxy was to help prevent the mounts from rattling and to prevent the carbon fibers from contacting the mount. I chose stainless steel mounts, and hope that this combined with the epoxy insulation will ensure against any galvanic reaction between the mount and tube.
I also squeezed the handles slowly and carefully. My goal was to just set the mount firmly without crushing the frame tube. The carbon is least strong against compression, and I don't want to crush this expen$ive $tuff. Anyhow, this appears to have been successful. There is no sign of looseness even with the a bottle cage mounted. There is no evidence that the tubes were crushed at all (I could feel when the mount was just drawn up against he tube - and stopped there, no cracks [even tiny hairlines] showed in close inspection of the epoxy near the mount, & no surface deformation was detected when tested with angles of reflection). Based on this, another mount was placed on the down tube with similar results.
The Black Pearl comes with with a front derailer clamp and specific torque instructions. So, the Campy derailer (w/35m clamp), that I planned to use, is a no go. I got an FSA compact instead. From a little way off it looks like a Chorus compact, its at least as light (published weight), and it doesn't cost much.
I mounted this and a purple anodized water bottle cage and showed the results to my wife (who doesn't impress easily when it comes to bikes). Her reaction was "Sexy Bike! But you've got to get rid of the purple cage." OK, everyone has different tastes, but the frame looks great. I took it with to spinning class and may have garnered two buyers (even without decals or clearcoat). So things are on track.
The cable stops still need to be mounted (I should have the right rivets by tomorrow), and I need to find a nearby painter. Then it'll be time to build and show it to the world.
Meanwhile, I've begun to cut tubes for a new steel frame for me. I'm trying a combo of Versus and Versus HT (depending on availability for desired sizes). This will use HJ mountain bike lugs for the top Head Tube and the seat cluster. The lower Head Tube and the BB will be Walter, resulting in a sloping top-tube 700c wheel design. The dropouts are forged steel with stainless steel fork tips and an HJ fork crown. The crown has 3 degrees of rake built in, limiting but not eliminating the bend in the fork legs. Everything is being built to accommodate fairly wide tires (I'll probably start with some 32's), and of course fenders.
The top and seat tube are mitered as is on seat stay. The downtube needs to be done, the seat tube needs to be cut to length (the seat lug caps the tube so that there is no extension), and the stays finished. Then its pin and braze. I'm looking forward to that.
More soon - but as I said, I've been busy.
Thursday, January 05, 2006
Has it been a month already?
It's been a month since the last post. Holidays, work, curling, family; it all adds up. So tonight we'll have a few updates, and then try to get on a more regular schedule of posting.
My jig is up and operational. For now, I'm experimenting with using it in a vice (vertically) and with lying on a table. I hope to have a trunnion for the back soon so that I can mount it in the Park stand.
It seems like the jig totally transforms the process of fitting tubes. Because they are not fitted one at a time - then brazed, we get to see the fit of the whole before brazing. It's also much easier to ensure that the fitted joint follows the plan. Working above a drawing is fine, but there's a lot of futzing around to make sure that the tubes parallel the plan and fit at the joints. I've actually started my current frame by mitering the top tube - which is backwards from my normal process. Tonight the seat tube will be fitted and tomorrow night the downtube. Then the front triangle can be brazed up out of the jig and we'll move to the rear triangle.
I'm also about to start a carbon (shock and horrors) from a kit by Deda. Actually, I'm going to try two kits. The first is a preformed monocoque front triangle to which seat and chainstays are attached. The second is a tube and lug kit that allows for some customization of fit. The idea is to not fight the currents. That is, I'd like to make a little money to support my frame-building. My guess is that these frames will be easier to sell at premium prices than steel (at least until such time as I establish a reputation as a great steel frame builders). I've already got 2 orders and a team interested in a common team bike. We'll soon know how good an entrepreneur I am. In any case, these frames will be sold under their own moniker in order to make sure that they don't undermine the values of my steel frames.
What else? A Park stand is now mounted to the workbench. My (mini) drill press is almost shaken apart from cutting tubing. It seems like a standard hole saw works as well or better than the fancy cutters I've tried. The edge of the cut needs some de-burring with a file when done with a hole saw, but the saw goes through the tube much faster than the cutters. I haven't given up looking for a better cutter, but so far this is where I'm at.
Kirk Pacenti has a nice old mill available for a reasonable price, but now isn't a good time for the investment, there's no space in the garage, and it weighs over half a ton. I keep telling myself that when I'm ready, another good deal will come along.
Well, it's time to get in the shop before going to curling.
See ya soon.